Case Studies
Case Studies
At IES2000, we're driven by a passion for perfect sound. Our expertise lies in sculpting spaces where every note sings and every word is crystal clear. But what truly fuels our excitement is the chance to collaborate. Whether it's architects, artists, or innovators, we thrive on working together to create unforgettable sonic experiences. Let's craft something extraordinary, together.
Every project gets 110%
ABB - The "Noisy Neighbor"
"These acoustical gates exceeded our expectations for aesthetics, functionality and performance." - Client
When ABB Power Systems had problems with noise levels at their Ocean City, Maryland installation, they were battling several factors. Noise above community ordinance levels was unacceptable, and ABB also had to contend with high winds at the location as well as ensuring the gates met security standards. ABB began searching for a supplier who could address the entire situation and provide a turn-key solution: design, engineer, craft and install a full solution that addressed all factors…..and ABB found IES-2000. We were able to design an automated sliding gate system that would withstand 140 MPH winds and operate in winds up to 75 MPH. ABB approved our designs, and the foundations were poured. The gate installation took our crew 5 weeks to complete from start to finish. The community noise ordinance required the site to comply to 65 dB(A) during the daytime hours and 55 dB(A) levels during nighttime hours. After the installation levels were below 45 dB(A) in all locations. IES-2000's solution provided a 15-17 dB(A) reduction from the louvered gates ABB had at the site originally.
Features
- Designed for 130 MPH wind load
- Gates will operate in winds up 75 MPH
- Utilizes STC 44 sound panels
- Meet community noise ordinance
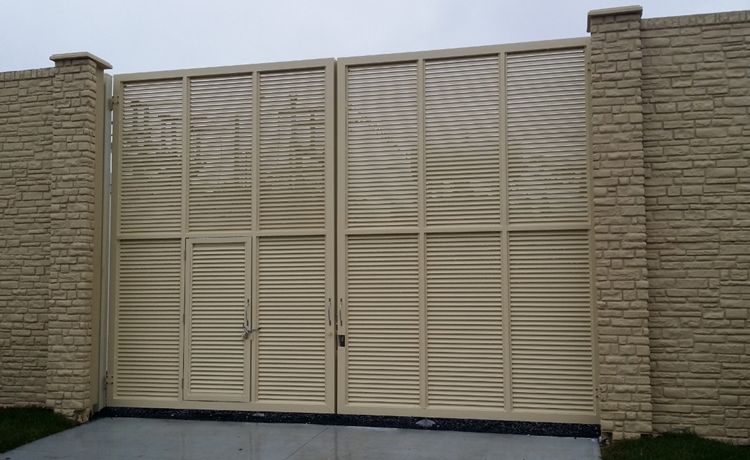
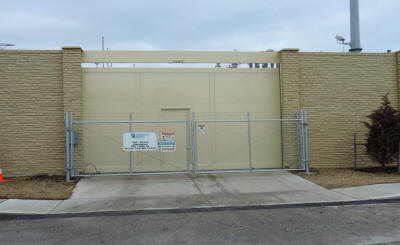
Mitigating Noisy Water Pumps for Military Application
"The pump covers provided the noise reduction and durability required for field operations." - Client
A pump manufacturer approached IES-2000 to design a solution to reduce noise being emitted from its water pump. The pump was emitting 98 dB(A), but noise reduction required this application to be less than 85 dB(A) at 3 feet. The unit was also required to be durable, easily removable, and collapsible to minimize storage space. IES-2000 had a pump sent to our factory so we could create a prototype unit. The pump required intake and exhaust ventilation baffles. The exhaust baffle was designed utilizing BA-13 with silicone facing to handle the heat. Two holes were created for piping, a flap was required for accessing the pull start as well as a flap required for re-fueling. Handles for removing the unit were added and the cover was labeled as specified. The cover designed by IES-2000 created a noise reduction of 13 dB(A). We also, developed a non-acoustic version of this cover using an 8-ounce canvas for applications that did not have the noise level requirement.
Features
- Ventilation baffles for air intake and exhaust
- Handles for easier carrying
- Collapsible design for easier storage
- Ease of access via specially designed flaps
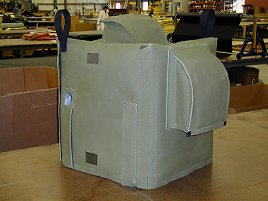
Plasma Spraying Operation Silenced with Noise Control Suite
"The noise reduction for these booths were between 35-44 dB(A)!" - Client
IES-2000 was contacted by IGS about our ability to reduce noise being emitted from their thermal spraying operations in their new headquarters. IGS had two thermal spray applications in their Production Area and one in the Test Lab that would require reducing the noise levels from 118-125 dB(A) to below 85 dB(A). The booth for the Test Lab was a 12’ x 12’ x 8’ high with a double door and large viewing window. The booths in the Production Area were combined into a suite to save floor space. The overall size was 42’ x 58’ x 10’ and 8’ high. The design included two large double doors, one 6070 double door, two 3070 single doors and windows. All windows received a pull down shade with weld tint for safety. The customer reported sound level readings of 81-83 dB(A) after all of the booths were installed while all thermal spray units were operating. The noise reduction for these booths obtained a 35-44 dB(A) reduction. The panels used on this project were rated as an STC 42 paired with STC 50 doors and windows. All necessary openings for duct work, electrical and other components were accommodated and sealed to maximize noise reduction.
Features
- 4” thick powder coated panels
- Large Double doors for equipment access
- Weld Tint for Windows
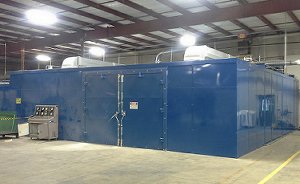
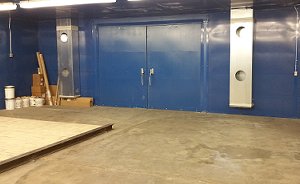